The 4” Condensate line had suffered from coating damage resulting in a localised corrosion area.
4″ Stabilised Condensate Line
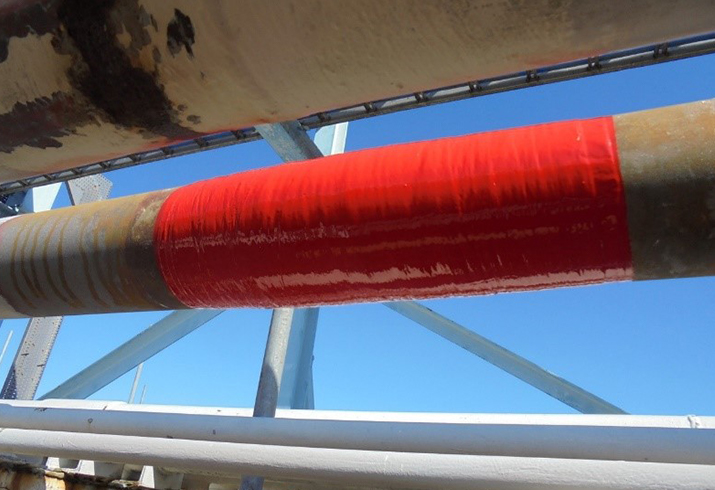
The 4” Condensate line had suffered from coating damage resulting in a localised corrosion area.
The cooling water line had suffered from severe external corrosion.
A hairline crack was identified on a 24″ GRE Seawater line at the flange, resulting in a leak.
The cooling water return line has been repaired using welded patches during a recent shut down.
The cooling water line has suffered from severe external corrosion.
This 6” hot oil transfer line has suffered from external corrosion resulting in several through wall leaking defects in a localised area.
The 4” Natural Gas vent line has suffered from external corrosion.
A 4 metre section of this line is suffering from external corrosion resulting in low remaining wall thickness.
The 24” line was found to be suffering from severe ‘full circumferential’ external corrosion over the full length of the spool
The line had been suffering from severe external corrosion at the soil / air interface resulting in several leaking defects at the 12 o clock position.