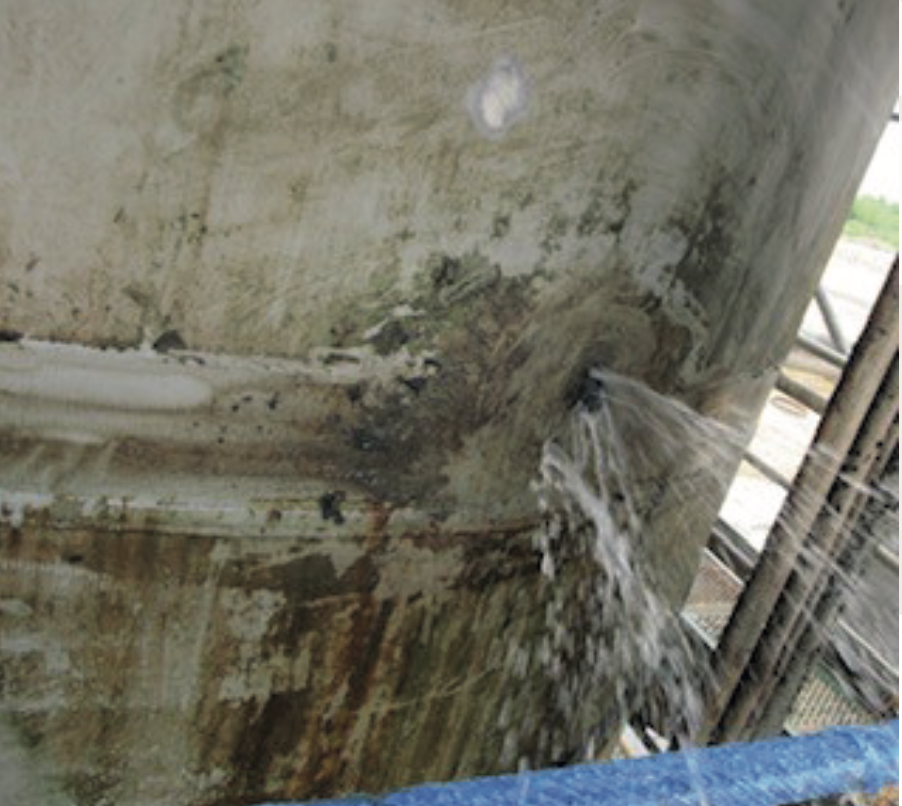
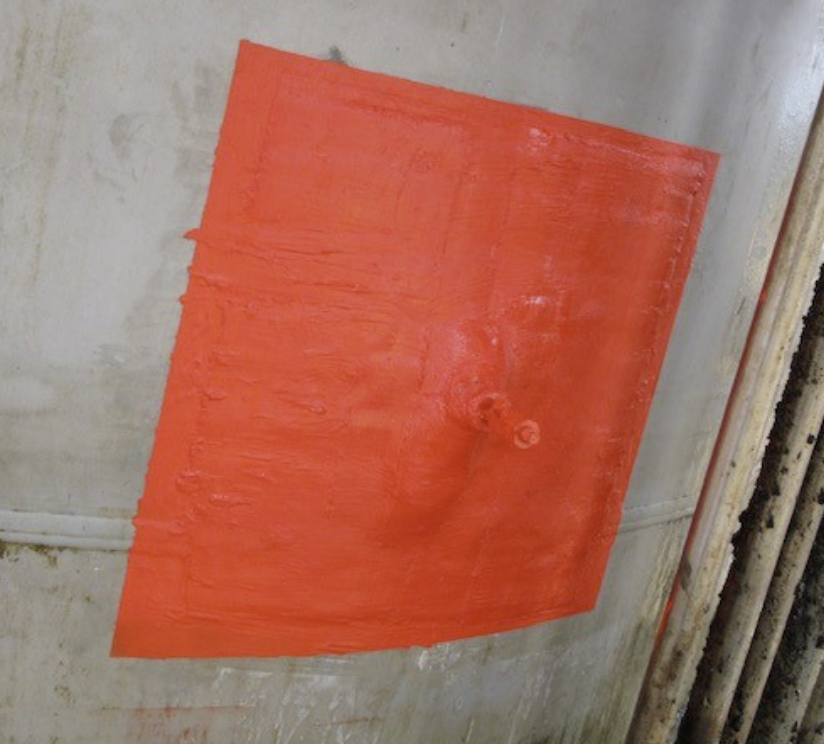
Nature of Defect
The water tank had suffered from possible internal acid corrosion. This has resulted in a leaking through wall defect on the outside of the vessel.
The Solution
Metalyte Pipeworks solution was to offer varied methods of leak seal options depending on the situation at the time of the repair. The options consisted of combining Herculyte resins and putties which are applied over the defect to seal the leak and plug the defect, or utilise the live leak Titan 505 system which utilises bespoke injectable sealants that are injected within the composite and seal the leak.
Repair Method
The first stage was to complete some initial surface preparation around the defect. Herculyte 106 epoxy was mixed and applied to the steel around the defect and allowed to cure. The technicians then attempted to plug the hole with Herculyte steel stick putty which unfortunately wasn’t 100% successful due to the water / oil mix. The technicians then moved on to the next method which included placing a bespoke divert directly over the leak and bonding it on to the steel using Titan 505 composite.
The technicians connected the injection system and injected the sealant into the divert. This was monitored to ensure the sealant was curing and the leak had stopped.
Once the defect was sealed, the technicians completed full surface preparation using the MBX bristle blaster over the full patched area. The prepared area is then washed down using clean away alcohol wash to remove any fine bits of dirt and dust.
The technicians then mixed the 2-part Dragon composite resins together and applied a bonding coat to the prepared area. The Dragon resin is then applied to the fibre glass cloth ensuring its fully saturated in resin. This role of saturated cloth was then cut into measured strips and applied to the repair area. The first 2 layers are applied in a 0° to 180° direction with the second 2 layers applied 90° to 270° direction and these layers are then compressed.
The composite was then left to cure until the following day. The compression materials were removed and the Shore D hardness readings taken to ensure full cure and compliance. Depending on the substrate and atmospheric temperatures, there is the option to utilise heating mats to increase the temperature to aid curing. The repair was then coated with 2 layers of UV protection pai